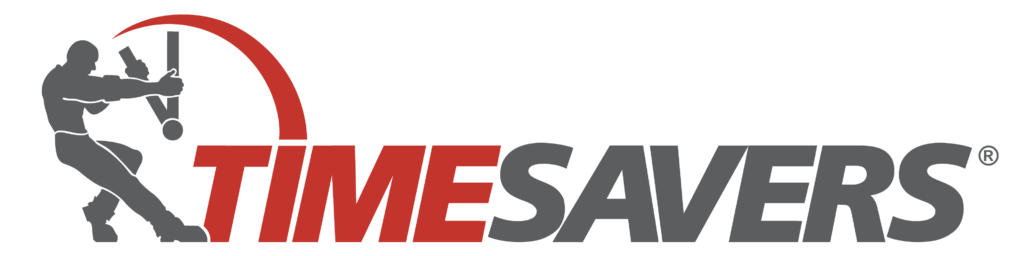
Timesavers’ metal sanders and deburring machines are fully customizable and built to suit your needs; offering a wider variety of solutions than most machinery brands. Regardless of how large or demanding your metalworking projects are, it’s imperative to find the best machines for each job. Timesavers provides the freedom to choose the exact features (including the number of heads, type of heads, wet-vs-dry – VIDEO, abrasives, etc.) with local support, service, and parts throughout the lifespan of your machine.
Timesavers machines offer multiple advantages, including higher productivity, more efficiency, and reduced waste – all of which contribute to supporting your bottom line.
Timesavers is one of the oldest, largest, and most advanced metal finishing machinery builders in the industry. Since 1946, they have partnered alongside manufacturers to overcome unique challenges and meet the industry’s ever-changing and growing demand for:
- Deburring
- Edge Rounding
- Finishing
- Precision Grinding
- Heavy Slag Removal
Deburring
Deburring refers to the process of smoothing the rough edges of a metal object or component. To some, a part is considered deburred when its vertical burr is removed. To others, a part isn’t fully deburred until it has a radius on each edge. No matter your end goal, consider the following Timesavers machines:
- The 1200 Series [9+disc]: These machines can be equipped with abrasive belts and rotary discs to eliminate vertical and lateral burrs simultaneously, gently rounding the edges of the part in the process. Ideal for deburring and finishing small metal parts.
- The Rotary Brush: A multi-directional brush machine that uniformly deburrs and finishes the edges of metal parts in a single pass. This process is completely harmless to surface coatings (such as cladding, zinc or laser film). Ideal for deburring the edges of laser-cut, punched or machined parts.
- Manual Grinder: A versatile machine with a rotatable head to swap between heavy grinding and edge rounding/deburring. Ideal for metalwork projects that require both deburring and grinding.
Edge Rounding
Edge rounding can refer to all actions that break the edge of a metal part. However, it is most commonly associated with the creation of a radius to the edge of a part. Rather than simply removing sharpness or deburring, edge rounding breaks a metal component’s edge in order to improve its surface for coating coverage and protect it from corrosion. Consider the following Timesavers for this application:
- The Rotary Brush: A multi-directional brush machine that uniformly deburrs and finishes the edges of metal parts in a single pass. Ideal for rounding the edges of laser-cut, punched or machined parts.
- Manual Grinder: A versatile machine with a rotatable head to swap between heavy grinding and edge rounding/deburring. Ideal for metalwork projects that require both grinding and edge rounding or deburring.
Finishing | Straight Grain Finish
Metal finishing refers to the process of altering a material’s surface to enhance its quality and aesthetic. Metal can also be finished to prepare its surface for paint adhesion or achieving a specific micro-inch finish.
The most common type of metal finish is a straight-line or grain finish for decorative purposes. In most cases, this process can be accomplished using standard abrasive belts. However, depending on the type of material, the desired result may require a combination of abrasive belts and brush heads. Consider the following Timesavers machines for your finishing needs:
- The Mini-Belt: A small and versatile machine that can be mounted to tables or workbenches. Ideal for light metal finishing and deburring projects.
- 1100 Series Wide Belt: A simple machine that’s easy to control and consumes minimal power. Ideal for deburring and finishing small metal parts.
- LYNX Series: These machines are equipped with high sanding belt horsepower and can be configured for metal finishing or deburring. Ideal for finishing rectangular tubing or flat bar stock.
- PUMA Series: These machines require minimum maintenance and upkeep, and both sides are easily accessible by operators. Ideal for deburring and finishing in a production setting and for 24/7 operations.